Batene: Energy boost for batteries
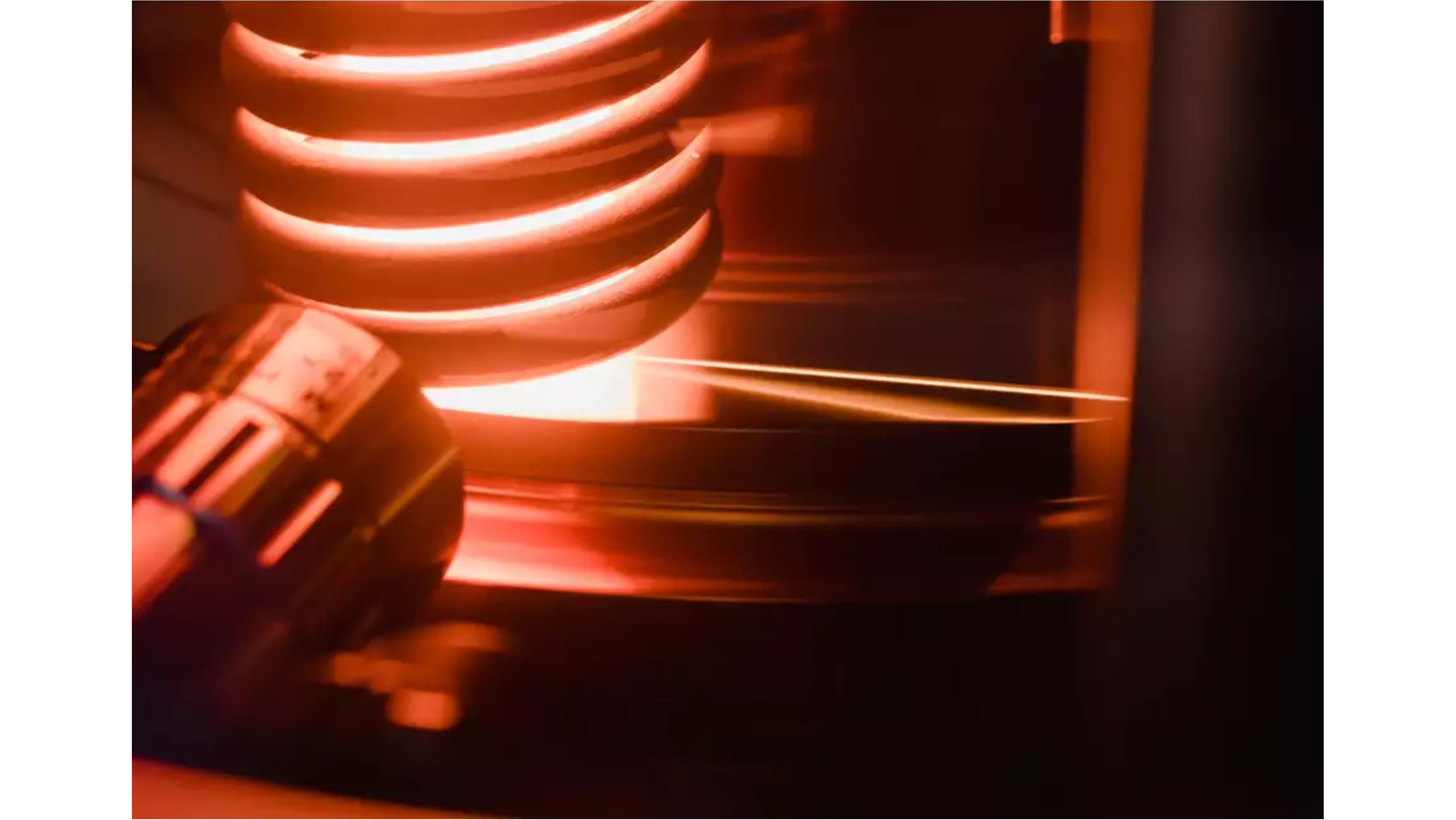
An electric car costs more than a comparable combustion engine because the battery is so expensive. And hardly any model gets as far on one charge as an average car on one tank of gas. Batene GmbH, a spin-off from the Max Planck Institute for Medical Research, wants to change this. The start-up is developing electrodes that could make batteries significantly more powerful, safer and cheaper – and is using a spinning technique to do so.
More Information in German below.
Batene: Energieschub für Batterien
Ein Elektroauto kostet mehr als ein vergleichbarer Verbrenner, weil die Batterie so teuer ist. Und mit einer Ladung kommt auch kaum ein Modell so weit wie ein durchschnittliches Auto mit einer Tankfüllung. Die Batene GmbH, eine Ausgründung aus dem Max-Planck-Institut für medizinische Forschung, will das ändern. Das Start-up entwickelt Elektroden, die Batterien deutlich leistungsfähiger, sicherer und billiger machen könnten – und setzt dabei auf eine Spinnerei.
Text: Peter Hergersberg
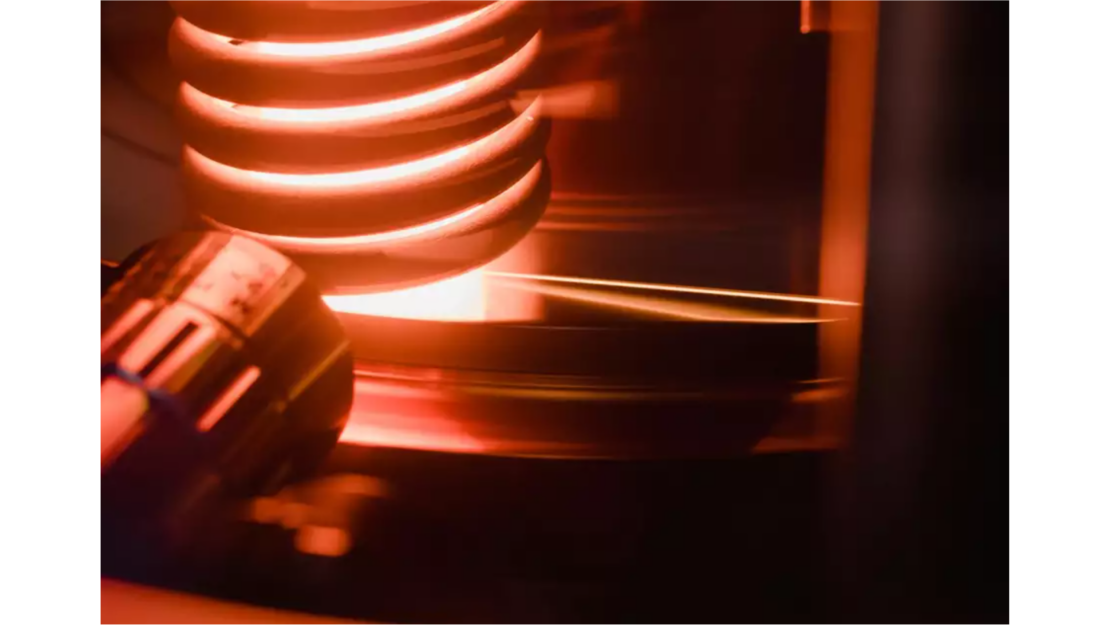
© Batene
Auf den Punkt gebracht
- Vliese statt Folien: Die Batene GmbH ersetzt die heute in Batterien üblichen metallischen Kontaktfolien durch Metallvliese. So ermöglicht sie es, bis zu zehnmal dickere Elektroden herzustellen, als heute verwendet werden.
- Leistungsfähiger und kostengünstiger: Dank der dickeren Elektroden steigt die Energiedichte von Batterien um mindestens 30 Prozent, möglich sind sogar 80 Prozent. Gleichzeitig vereinfachen die metallischen Vliese die Herstellung und könnten die Kosten für eine Batterie um bis zu 40 Prozent senken.
- Auf dem Weg zur Massenproduktion: Batene kooperiert mit namhaften Automobilherstellern und plant derzeit eine Pilotanlage, um zu zeigen, dass sich Vlieselektroden großtechnisch herstellen lassen.
Spinnen hat hier Tradition: Wo mehr als 100 Jahre lang ein Textilunternehmen Garn produzierte und Tuch webte, zieht ein Start-up heute buchstäblich Fäden für die Energiewende. Die Batene GmbH, ein Spin-off des Max-Planck-Instituts für medizinische Forschung in Heidelberg, hat einen Weg gefunden, Metalldrähte, deutlich feiner als ein menschliches Haar zu spinnen und zu fluffigen Vliesen zu verarbeiten. Diese sollen die Kontaktfolien in heutigen Batterieelektroden ersetzen und die Energiespeicher nicht nur wesentlich leistungsfähiger, sondern auch deutlich kostengünstiger machen.
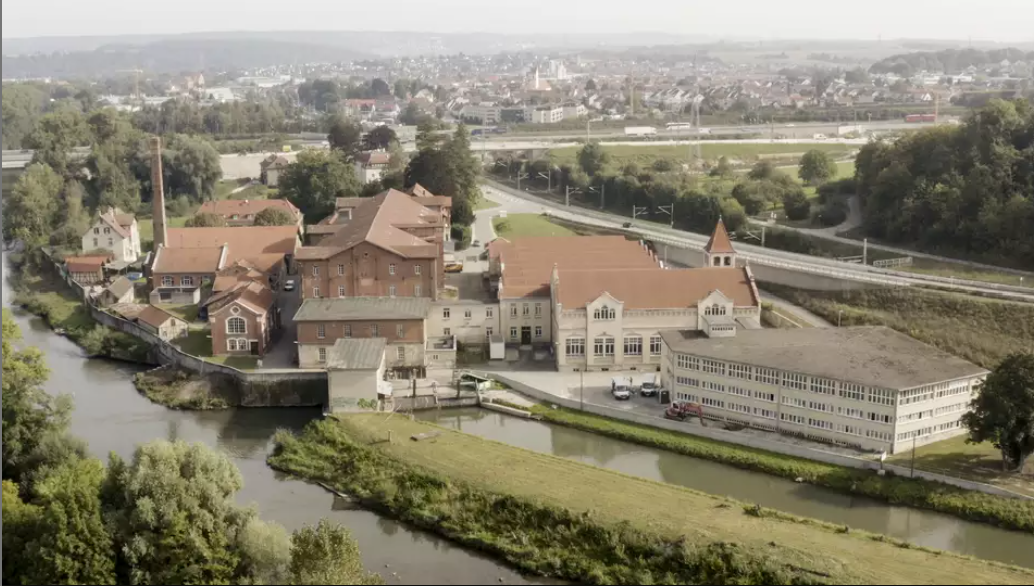
© HOS Gruppe
Wer sich vom Zentrum Wendlingens, einer baden-württembergischen Kleinstadt, kommend dem Firmensitz der Batene nähert, kann das rote Backsteingebäude nicht übersehen. Mit seinen drei Geschossen und großen Fenstern dominiert es das Areal am Neckar – erkennbar Industriearchitektur aus dem 19. Jahrhundert. Rundherum fügen sich Anbauten jüngeren Datums mit ockergelben Klinkerfassaden in den Komplex. Seit 1861 ist hier das Textilunternehmen Heinrich Otto gewachsen, mit Betriebswohnungen, eigener Kirche und einem Wasserkraftwerk, das heute noch Strom produziert. Inzwischen belegt ein Nachfolgeunternehmen nur noch einen kleinen Teil der 20 000 Quadratmeter Gewerbefläche .
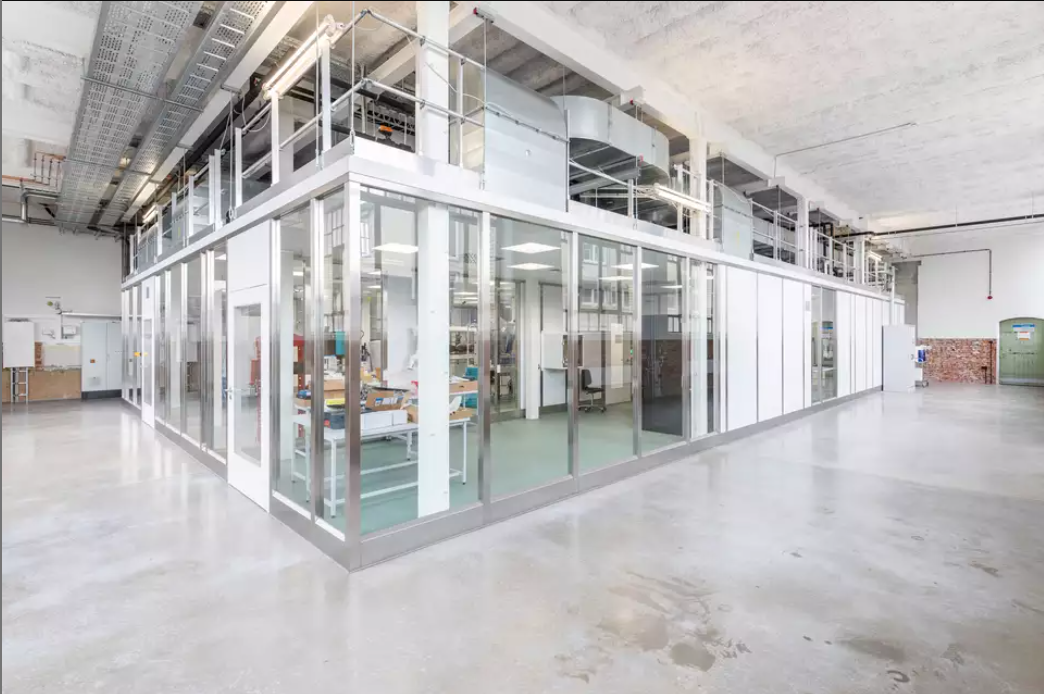
© Nguyen T.D. Thanh
Joachim Spatz, Direktor am Max-Planck-Institut für medizinische Forschung in Heidelberg und Gründer der
Batene, führt durch die loftartigen Räume, die von der Betriebsamkeit der Vergangenheit und auch deren Niedergang gezeichnet sind. Manche Teile der Gebäude stehen noch leer, die Wangen der abgenutzten Holztreppen, die dorthin führen, sind von staubigen Spinnweben verhangen. Auf anderen Flächen haben sich bereits Start-ups eingerichtet. Und bei Batene ist der Kontrast zwischen Vergangenheit und Zukunft besonders groß: In die Hallen mit industriellem Vintage-Charme hat das Unternehmen Hightech-Labore und sogar einen Trockenraum, einen Raum im Raum mit großen Fensterflächen, gesetzt. Hier untersuchen die Mitarbeitenden, wie sich mit der Batene-Technik effizient und ökonomisch Batterieelektroden herstellen lassen. Joachim Spatz hat das Unternehmen 2023 gemeinsam mit Martin Möller, Co-Geschäftsführer, und Thanh Nguyen, Co-Geschäftsführerin und Finanzvorstand des Unternehmens, gegründet. Das Start-up stellt noch laufend neue Mitarbeiterinnen und Mitarbeiter ein, derzeit sind es 17, die teilweise nach ihrer Promotion in der Max-Planck-Abteilung von Joachim Spatz zu Batene gewechselt sind. Weitere zwölf Personen erforschen die Grundlagen der Technik am Heidelberger Max-Planck-Institut.
Schmelzspinnen auf einer Drehscheibe
In einem karg eingerichteten Raum, der noch nicht komplett renoviert ist und teils als Büro, teils als Besprechungsraum dient, erklärt Joachim Spatz, wie er als Direktor des Max-Planck-Instituts für medizinische Forschung dazu gekommen ist, sich mit Batterietechnik zu beschäftigen. „Als Physiker habe ich mich schon immer dafür interessiert, wie sich Materialien strukturieren lassen und wie sich ihre Oberfläche vergrößern lässt, weil das die Funktion der Materialien verändert und in vielen Bereichen relevant ist.“ Unter anderem hat er untersucht, wie biologische Zellen auf strukturierte Oberflächen reagieren. Bei den hauchdünnen Metallfäden ging es aber zunächst nur um die Methode an sich. Dabei gibt es bereits seit den 1970er-Jahren ein Gerät, in dem eine rotierende Walze aus einem Strahl flüssigen Metalls dünne Bänder zieht. Dieses als Schmelzspinnen oder Meltspinning bekannte Verfahren hat Joachim Spatz buchstäblich umgeworfen: „Ich habe mir überlegt, wie die Kräfte bei einem Meltspinning wirken“, sagt der Physiker. „Daraus ist dann die Idee entstanden, dass man anstelle von Bändern feinere Metallfäden erhält, wenn das flüssige Metall nicht auf eine Walze, sondern auf eine rotierende Scheibe fließt. Außerdem kann man in diesem Aufbau die Faserlänge besser kontrollieren.“ Aktuell erzeugt Batene auf diese Weise Fasern, die im Extremfall nur zwei hundertstel Millimeter breit und ein hundertstel Millimeter dick sind. Zum Vergleich: Ein menschliches Haar hat einen Durchmesser von etwa einem zehntel Millimeter.
Das Ziel ist ein 3D-Versorgungsnetz für Ladungsträger, über das sich Batterien effizient laden und entladen lassen. – Joachim Spatz
Wie das in der Praxis aussieht, zeigt Louise Kaeswurm, Materialwissenschaftlerin und Mitarbeiterin von Batene, in einem der Produktionslabore. Durch eine Art Bullauge in einer Vakuumapparatur aus Edelstahl ist die Drehscheibe zu sehen, die an einen Plattenspieler erinnert. „Hier dreht sich aber nur ein äußerer Ring, der mit Wasser gekühlt wird“, erklärt Louise Kaeswurm. In der rechten hinteren Ecke hängt über dem Tellerrand, etwa so groß wie eine Tasse und hell glühend, ein Tiegel. Aus ihm rinnt das flüssige Metall auf den kalten Tellerrand, der mit rund 30 Umdrehungen pro Sekunde rotiert, wird durch die Drehung blitzschnell in die Länge gezogen und erstarrt. So fliegen die Fäden – mal meterlang, und mal eher als kurze Schnipsel, je nachdem ob die Forschenden das Metall als dünnes Rinnsal oder in winzigen Tropfen aus dem Tiegel laufen lassen. Am Ende entsteht eine metallische Watte, die sich auch beinahe so anfühlt, so fein sind die gesponnenen Fasern. Ein paar Schritte weiter steht schon das Spinnrad der nächsten Generation, ein unscheinbarer Metallwürfel, der weniger Platz braucht als eine Mikrowelle. Es soll die Fäden schon im Fließbandverfahren herstellen: Das Metall, aus dem das feine Garn entsteht, wird kontinuierlich in den Apparat nachgeführt, sodass das Spinnrad unaufhörlich Fäden produziert.
Video über das Siegerteam Batene
https://www.youtube.com/watch?v=rwESH-5dh8U
Lösung für das Dilemma der Batterieindustrie
Als Joachim Spatz den neuartigen Schmelzspinner 2014 erfunden hatte, ließ er ihn auch gleich patentieren. Denn ihm war klar, dass es für eine Massenproduktion so feiner Metallfasern einige Anwendungen geben könnte: in Katalysatoren für chemische Reaktionen, die möglichst viel Oberfläche brauchen, um effizient zu arbeiten, als elektromagnetische Abschirmung oder als Filtermaterial etwa. „Irgendwann war dann die Idee da, Vliese aus den feinen Metallfäden als Kontakte in Batterieelektroden zu verwenden“, sagt Spatz. Denn mit ihnen könnte sich ein Problem heutiger Batterien in den Griff bekommen lassen: Das eigentliche Speichermaterial, im Fachjargon Aktivmaterial genannt, leitet Strom und Lithiumionen extrem schlecht.
Damit aktuelle Batterien überhaupt in akzeptablen Zeiten geladen werden können, stapeln sich in ihnen unzählige dünne Zellschichten übereinander, die jeweils nur rund zwei zehntel Millimeter dünn sind, sodass die Ladungsträger keine weiten Wege zu den Kontakten zurücklegen müssen. So läppert sich der Anteil der Kontaktfolien und des Separatormaterials, das Plus- und Minuspol voneinander trennt, zu einer erklecklichen Menge. Die braucht Platz und bringt Gewicht mit, trägt aber nichts zur Speicherung bei. Deshalb müssen Batteriehersteller heute stets einen Kompromiss zwischen Energiedichte, also der Speicherkapazität pro Masse, und Lade- beziehungsweise Entladegeschwindigkeit eingehen. Wenn eine Batterie in kurzer Zeit viel Leistung bringen muss, in einem Sportwagen beispielsweise oder beim Start eines Elektrohubschraubers, entscheiden sie sich für besonders dünne Zellen. Das geht dann auf Kosten der Speicherkapazität, oder die Batterie wird sehr groß und schwer.
Metallvliese ermöglichen zehnmal dicker Batteriezellen
„Die Versorgung eines Materials mit Ladung über zweidimensionale Schichten ist jedoch in keiner Weise effizient“, sagt Joachim Spatz und verweist auf das Vorbild der Natur: Sie versorge Organismen über ein dreidimensionales Netzwerk an Gefäßen. „Und das ist das Ziel unserer Technologie: ein 3D-Versorgungsnetz für Ladungsträger, über das sich Batterien effizient laden und entladen lassen.“ Vliese aus Metallfasern, die als Kontaktmaterial das gesamte Aktivmaterial einer Elektrode durchdringen, heben das Dilemma heutiger Batterien auf. Denn sie ermöglichen bis zu zehnmal dickere Batteriezellen, die ihre Ladung trotzdem blitzschnell aufnehmen und abgeben. So lassen sich in Batterien aus den dickeren Zellen 60 Prozent des Metalls für die elektrischen Kontakte und auch ein Großteil des Separatormaterials einsparen. Zudem sind die dickeren Zellen stabiler als die hauchdünnen Zellen heutiger Akkus. Das ist ein wichtiger Grund, warum die Batene-Technik Batterien auch sicherer macht.
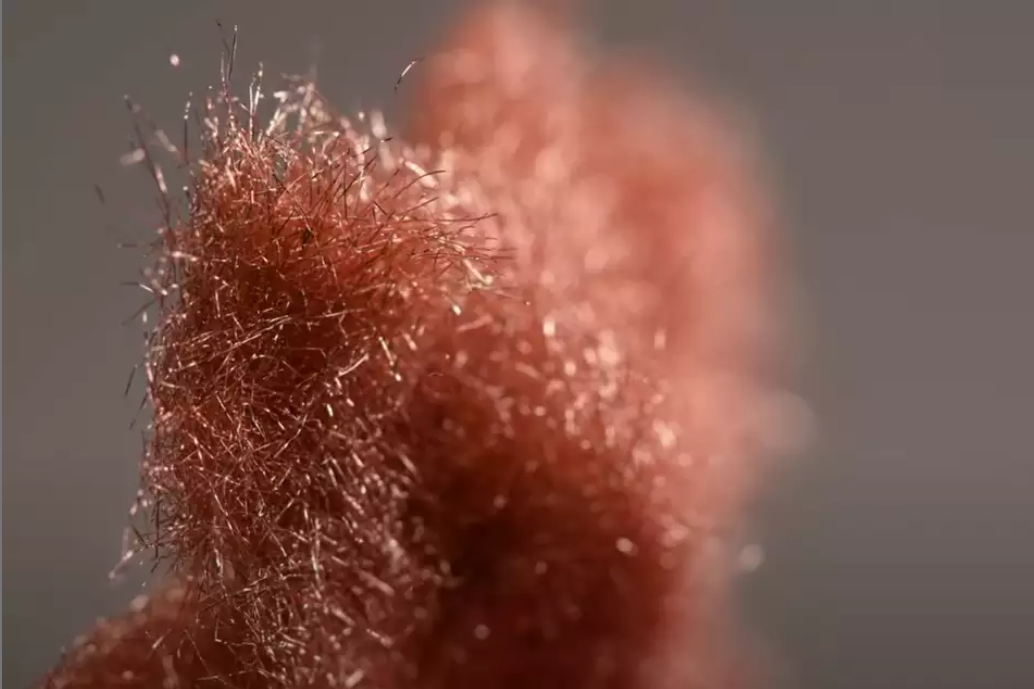
© Batene
Die Vliese stellen Johannes Hirte und Daniel Hotz her, indem sie ein Knäuel der Metallfasern in ein Flüssigkeitsbad tauchen und da hindurch Luft strömen lassen. Dabei geht es in dem Behälter zu wie in einem Topf mit sprudelnd kochendem Wasser. Die Prozedur entwirrt die Fasern, sodass diese sich am Ende als metallisches Vlies am Boden absetzen. Auf ganz ähnliche Weise produziert die Papierindustrie aus Watte von Zellulosefasern dünne Bögen. Sie hat den Prozess so optimiert, dass ein Fließband die Pulpe aus Zellulosefasern und Wasser in einem dünnen, beliebig langen Band aus dem Sprudelbecken schöpft. „Dahin wollen wir bei der Herstellung unserer Metallvliese auch kommen“, sagt Martin Möller. Das Vliesband soll dann auch direkt durch einen Ofen geschoben werden, in dem eine Temperatur knapp unterhalb der Schmelztemperatur des jeweiligen Metalls herrscht. Heißer darf es nicht sein, sonst fiele das feine Metallgespinst sofort in sich zusammen und übrig bliebe nur ein Film flüssigen Metalls.
Eine Schnellstraße für Lithiumionen
Trotz der eigentlich zu niedrigen Temperatur werden die feinen Metallfasern an ihren Berührungspunkten miteinander verschweißt. Denn die Forschenden können sich hier eine Eigenheit der gesponnenen Metallfäden zunutze machen: Das flüssige Metall wird beim Aufprall auf dem gekühlten Spinnrad quasi schockgefrostet und erstarrt in der atomaren Unordnung des flüssigen Zustands – physikalisch gesprochen enthalten die gesponnenen Fäden ziemlich viel eingefrorene Energie. Daher werden die Atome schon knapp unterhalb des Schmelzpunktes beweglich und bilden mit benachbarten Drähten feste Verbindungen – buchstäblich eine glückliche Fügung. Das ist aber nicht der einzige physikalisch-chemische Umstand, der Joachim Spatz und seinem Team zu Hilfe kam, und manchmal kam die Unterstützung durch die Natur auch völlig unerwartet.
So haben die Forscherinnen und Forscher anfangs gar nicht abgesehen, wie stark die Vliese den Ladungsaustausch mit dem Aktivmaterial beschleunigen und somit die Kapazität von Batterien erhöhen. Klar, Elektronen verteilen sich schnell über das Metallgespinst in der Elektrode und dringen von dort flugs ins Aktivmaterial ein. Aber auch ihre Gegenstücke, die positiven Ionen, heute meist Lithiumionen, flutschen dank der Metallvliese bis zu 100-mal schneller durch das Aktivmaterial als in den gängigen Folienbatterien. Wie kann das sein? Schließlich können sie ja nicht durch die Metalldrähte wandern wie Elektronen. Allerdings sammeln sich direkt an der Metalloberfläche Elektronen, und auf der Oberfläche setzen sich zum Ladungsausgleich Lithiumionen ab. Diese elektrische Doppelschicht, die sogenannte Helmholtzschicht, wirkt wie eine Schnellstraße für die Lithiumionen. „Die Helmholtzschicht war schon lange bekannt“, sagt Joachim Spatz. Dass sie den Ladungstransport in Batterien beschleunigt, hat uns aber überrascht und war gänzlich neu.“
Batterien mit mindestens 30 Prozent mehr Energiedichte
Wie leistungsfähig die Batteriezellen sind, die den Strom mit Vlies- statt Folienelektroden ableiten, testen Jan Tenbusch und Maximilian Hackner im Trockenraum, den Batene in das alte Fabrikgebäude gesetzt hat. Die Luft ist darin so trocken, dass ein Mensch ohne Schutzanzug darin pro Stunde einen Liter Flüssigkeit verliert. Die Luftfeuchtigkeit muss so niedrig sein, damit das Aktivmaterial der Batterieelektroden keinen Schaden nimmt. Hier stellen Jan Tenbusch und Maximilian Hackner aus Metallvlies und einer Paste des Aktivmaterials die Elektroden her: Kupfervlies und Graphitverbindungen für den Minuspol, Aluminiumvlies und anorganische Verbindungen für den Pluspol. Die Elektroden fügen sie dann zu Batteriezellen zusammen und prüfen deren Vitalfunktionen mit einem Batterietester, der die Zellen 1000-mal lädt und entlädt.
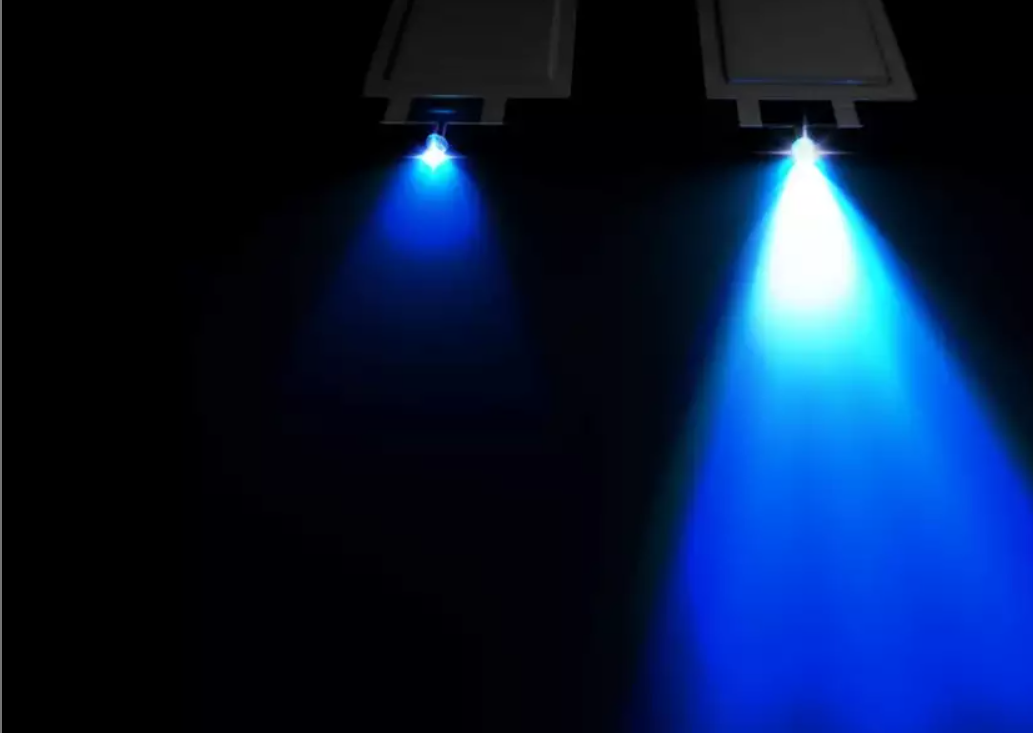
© Batene
1000 komplette Ladezyklen sind für ein Elektroauto schon viel. Denn selbst mit einer kleinen Batterie, die nur eine Reichweite von gut 300 Kilometern bringt, kann ein Auto dann schon mehr als 300 000 Kilometer fahren. Derzeit haben die Batene-Zellen einige Hundert Ladezyklen absolviert. Die aktuellen Testergebnisse belegen bereits, dass die Energiedichte der BateneZellen um 30 Prozent steigt und auch über Hunderte Ladezyklen stabil bleibt. Doch da ist noch mehr drin. Denn in Vlieselektroden kann Batene auch Aktivmaterialien verwenden, die zwar ausgesprochen hohe Energiedichten ermöglichen, deren Leitfähigkeit aber zu schlecht ist, um in heutigen Batterien überhaupt eingesetzt werden zu können. Das Batene-Team rechnet damit, dass sich die Energiedichte mit solchen Materialien bei schnellen Lade- und Entladegeschwindigkeiten, wie sie etwa bei Elektroautos und viel mehr noch bei Hubschraubern mit Elektroantrieb gefragt sind, im Vergleich zu heutigen Akkus um bis zu 80 Prozent steigern lässt.
Bis zu 40 Prozent niedrigere Produktionskosten
Aus Sicht der Batteriehersteller ist die erhöhte Energiedichte aber nicht der einzige Vorteil der Batene-Technik, vielleicht nicht einmal der entscheidende. „Die Unternehmen, mit denen wir im Gespräch sind, interessieren sich für unsere Technik vor allem, weil sie eine deutlich einfachere und kostengünstigere Produktion von Batterien ermöglicht“, sagt Thanh Nguyen. Zudem ist die Herstellung der zarten Zellen heutiger Batterien sehr fehleranfällig. Daher erfordert es große Erfahrung, um dabei nicht zu viel teuren Ausschuss zu produzieren. Gerade in dieser Hinsicht haben asiatische Firmen einen beträchtlichen Vorsprung.
Unternehmen interessieren sich für unsere Technik vor allem, weil sie eine kostengünstigere Produktion ermöglicht. – Thanh Nguyen
Bei der Fabrikation der Dünnschichtelektroden müssen die Unternehmen einen vollkommen glatten Film des aufgeschlämmten Aktivmaterials nahtlos auf die Kontaktfolie aufbringen. Dafür benötigen sie zum Teil krebserregende und umweltschädliche Lösungsmittel. Und das heißt: Sie müssen nicht nur Trockenstraßen errichten, die ganze Hallen füllen, damit die Lösungsmittel aus den hauchdünnen feuchten Schichten verdampfen können. Sie müssen die giftigen Substanzen auch zurückgewinnen, ohne dass ihre Mitarbeiterinnen und Mitarbeiter die Dämpfe einatmen. Das macht die Sache sehr aufwendig und teuer. Viele Batteriehersteller suchen daher nach Wegen, das Aktivmaterial trocken zu verarbeiten. Bislang verwendet zwar auch Batene Lösungsmittel, um die Aktivmaterialien in die Vliese einzubringen. Doch Joachim Spatz ist sicher, dass sich die Produktion der Batene-Elektroden tatsächlich trocken legen lässt. „Mit der Trockenbefüllung können wir vermutlich 30 bis 40 Prozent der Produktionskosten sparen, und die Anlagen brauchen ein Drittel weniger Platz.
Kooperationen mit namhaften Automobilherstellern
Energieschub und Kostenersparnis – da werden auch große Akteure im Batteriegeschäft aufmerksam: So kooperiert Batene inzwischen mit namhaften Automobilherstellern. Derzeit wirbt das Start-up Mittel für eine Pilotanlage ein, um zu zeigen, dass sich die Vlieselektroden auch im großen Stil herstellen lassen. Mit der Produktion dieser Anlage will das Start-up erste Kunden beliefern. Außerdem sollen hier Prototypen für die Automobilunternehmen entstehen, die darauf aufbauend dann Gigafabriken für ihren Massenbedarf errichten.
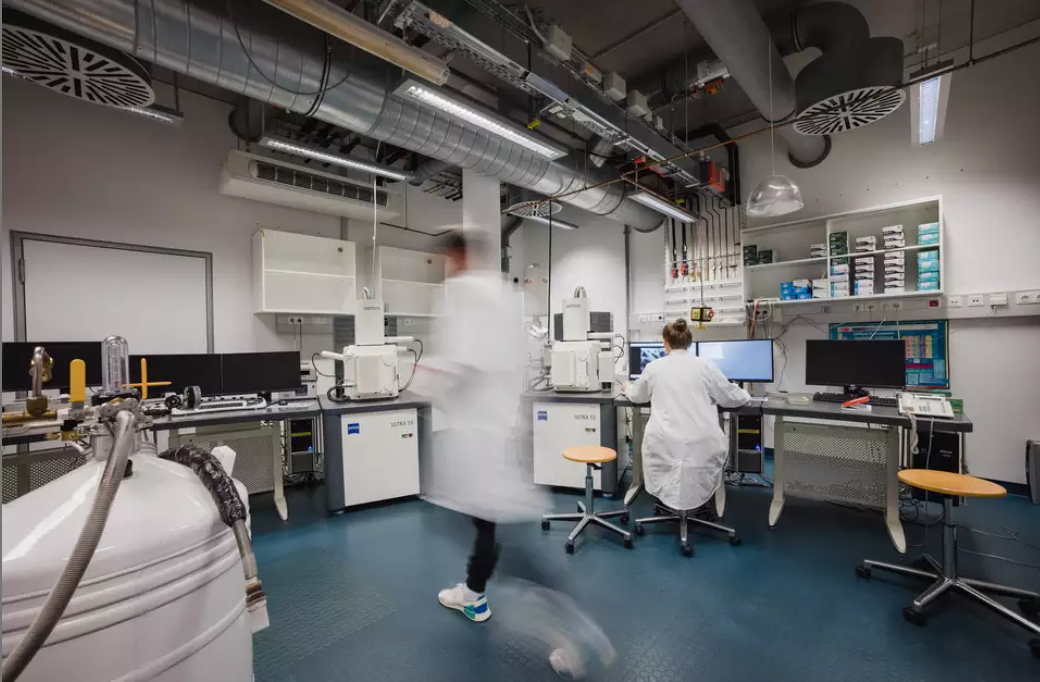
© Batene
Dass der Absatz von Elektroautos 2024 in Deutschland stark eingebrochen ist, bereitet dem Team von Batene zwar Sorgen, aber: „In anderen Ländern boomen Elektroautos nach wie vor, nicht nur in Asien, sondern auch in Europa“, sagt Thanh Nguyen. „Die E-Mobilität wird kommen.“ Und das nicht nur im Personenverkehr, sondern auch im Schwerlastverkehr, für den lange noch Wasserstoff oder synthetische Kraftstoffe als möglicher Ersatz für Diesel gehandelt wurden. Laut dem amerikanischen Marktforschungsunternehmen S&P Global Market Intelligence hat sich das Wachstum der weltweiten jährlichen Batterieproduktion zwar etwas abgeschwächt und soll für 2025 bei Zellen mit einer Speicherkapazität von rund 1,4 Terawattstunden liegen – das entspricht etwa der Strommenge, die Einwohner einer deutschen Millionen-Stadt jährlich an Strom verbrauchen. Doch die US-Analysten gehen davon aus, dass sich die Batterieproduktion schon bis zum Jahr 2030 etwa vervierfachen wird.
Geeignet für verschiedene Batterietypen
Für das Unternehmen stellt es auch kein Problem dar, dass der Batteriemarkt sehr dynamisch ist, um es im Wirtschaftsjargon zu formulieren. Bis vor Kurzem galt ein Lithium-Ionen-Akku mit einem Pluspol aus Nickel, Mangan und Kobalt als erste Wahl für leistungsfähige E-Autos. Doch Nickel und Mangan sind teuer, Letzteres wird zudem unter problematischen sozialen und ökologischen Bedingungen gewonnen. Inzwischen aber fahren vor allem viele chinesische Elektrofahrzeuge mit Lithium-Eisenphosphat-Batterien. Und auch Natrium- Ionen-Batterien, die kein teures und schlecht verfügbares Lithium mehr brauchen, sind im Rennen, vor allem als große stationäre Speicher für erneuerbaren Strom. Sie liefern aber auch bereits den Strom für erste Elektroautos. Und dann gibt es auch noch Feststoffbatterien, die ohne flüssige Elektrolyte auskommen und daher sicherer und kompakter als die heute gängigsten Akkus sein sollen. Welcher Zelltyp sich am Ende durchsetzen wird – vermutlich werden es je nach Anwendung verschiedene sein –, ist noch offen. Für Batene ist das aber egal. „Unsere Technik ist für alle Zelltypen und Zellmaterialien geeignet“, sagt Joachim Spatz. Nicht zuletzt deshalb ist er zuversichtlich, was die Aussichten für Batene anbelangt: „Mit unserer Technik haben wir die Chance, den Vorsprung der asiatischen Hersteller aufzuholen und besser zu sein.“
Glossar
- Aktivmaterial speichert in einer Batterie die Energie. Dabei wird beim Entladen chemische in elektrische Energie umgewandelt, beim Laden elektrische in chemische Energie. In Lithium-Ionen-Akkus werden derzeit hauptsächlich Graphitverbindungen für den Minuspol und anorganische Verbindungen für den Pluspol verwendet.
- Dünnschichtelektroden bestehen aus einer dünnen Metallfolie als Kontaktmaterial, auf der das Aktivmaterial aufgebracht wird. In einem Lithium-Ionen-Akku am Minuspol Kupferfolie und am Pluspol Aluminiumfolie. Zellen aus solchen Elektroden sind etwa zwei zehntel Millimeter dick.
- Vlieselektroden können etwa zehnmal dicker sein als Dünnschichtelektroden, weil in ihnen das Aktivmaterial von einem metallischen Vlies durchdrungen wird. So lassen sich in Batterien bis zu 60 Prozent Metall des Kontaktmaterials einsparen.